The Role of Foam Control in Enhancing Item High Quality and Performance
Foam control is an often-overlooked yet crucial part in the pursuit of product quality and functional effectiveness across varied industries. This conversation will check out the diverse influence of foam on both product integrity and production procedures, elevating essential concerns regarding the techniques that can be employed to enhance foam control.
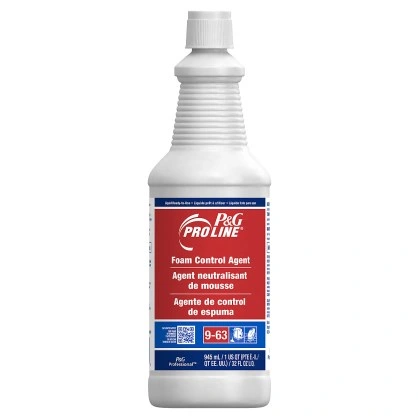
Comprehending Foam Formation
Foam development is an intricate phenomenon that can substantially affect product quality and functional performance across numerous sectors. It happens when gas bubbles end up being entraped in a fluid, leading to the development of a frothy structure. Several elements add to this process, including the physical and chemical properties of the fluid, the presence of surfactants, and the problems under which blending takes place. Comprehending these variables is vital for taking care of foam properly.
The liquid's viscosity and surface area stress play pivotal functions in foam stability. Surfactants, for example, can reduce surface tension, promoting bubble development however also improving foam stability, which can be problematic in particular applications. Mechanical anxiety, temperature level fluctuations, and the presence of impurities can worsen foam generation, making it essential to keep track of these aspects during production processes.
Industries such as food and drink, pharmaceuticals, and chemical production need to be particularly watchful pertaining to foam control. By understanding the hidden mechanisms of foam formation, organizations can carry out targeted techniques to reduce its effects, therefore maintaining functional performance and ensuring constant product efficiency.
Influence on Product Quality
The visibility of foam can considerably jeopardize item top quality across different industries. In manufacturing processes such as food and drink, pharmaceuticals, and cosmetics, extreme foam can cause irregular product formulas. In food manufacturing, foam may catch air, impacting appearance and flavor, which can inevitably change consumer assumption and fulfillment.
Furthermore, foam can prevent the harmony of paints and coatings, leading to defects like bubbles and unequal surfaces. In pharmaceutical applications, foam can disrupt the accurate dosing of liquid medications, possibly impacting healing effectiveness and client safety. These high quality issues not just lessen the end product's charm yet can additionally cause costly recalls and damages to brand online reputation.
Additionally, the presence of foam can complicate top quality control steps, making it hard to achieve accurate measurements and consistent results. Efficient foam control not just mitigates these risks however likewise enhances total product quality by ensuring that formulations meet strict industry criteria. By investing in foam control methods, firms can safeguard their items, boost customer complete satisfaction, and maintain a competitive edge in the marketplace.
Operational Difficulties From Foam
Effective operations in various sectors can be severely interrupted by the existence of foam, which presents multiple difficulties throughout manufacturing procedures. Foam can impede mixing and reaction times, restraining the performance of chemical processes. In industries such as food and drink, foam development can result in imprecise fill levels, resulting in item waste and inconsistencies in product packaging.

In settings where health is vital, such as drugs and food processing, foam can make complex cleansing methods, producing concealed tanks for impurities. This not only elevates quality problems yet additionally can result in conformity issues with regulatory requirements.
Furthermore, the mental effect on drivers can not be ignored; excessive foam can produce a chaotic work setting, resulting in reduced morale and performance. In summary, dealing with the operational challenges presented by foam is crucial to preserving effectiveness and item top quality in various markets.
Strategies for Efficient Foam Control
Exactly how can markets successfully minimize the obstacles posed by foam? Effective foam control techniques are essential for enhancing item quality and functional performance.
Along with chemical options, process optimization plays a vital role in foam monitoring. Industries can analyze and readjust specifications such as blending temperature, speed, and pressure to lessen foam generation. Applying equipment adjustments, like installing foam-breaking tools or adjusting storage tank design, can further help in reducing foam levels.
Normal monitoring and evaluation of foam behavior within manufacturing processes are additionally essential. Making use of innovative sensors and analytics can provide real-time information, enabling timely interventions and adjustments. Staff training is similarly important; guaranteeing that personnel are educated about foam characteristics and control strategies can lead to positive foam administration.
Instance Researches and Market Applications
While numerous sectors deal with special challenges associated with foam control, case research studies expose that customized techniques can dramatically improve both item high quality and functional performance. In the pharmaceutical field, for example, a leading manufacturer implemented a personalized foam control approach that decreased foam formation during fermentation procedures. This advancement not only improved return by 15% yet also decreased contamination threats, making sure greater product stability.
Likewise, in the food and beverage market, a significant dairy products producer faced excessive foam throughout pasteurization - Foam Control. By introducing a specialized antifoam representative, they reduced handling time by 20%, which straight equated to increased throughput my link and decreased power usage. The this link application of foam control gauges ensured consistent item appearance and taste, enhancing brand name loyalty
In the chemical manufacturing sector, an instance study highlighted the effective application of foam control in wastewater therapy procedures. The application of a real-time tracking system enabled operators to readjust antifoam dosage dynamically, resulting in a 30% decrease in chemical usage and improved effluent top quality.
These case studies illustrate the varied applications of foam control across sectors, highlighting its critical role in boosting item quality and operational efficiency.
Verdict
In conclusion, effective foam control is essential to enhancing product high quality and functional effectiveness throughout numerous markets. Eventually, focusing on foam control adds to enhanced productivity, guarding brand name track record, and boosting customer complete satisfaction, highlighting its significance in high quality guarantee within producing procedures.
Foam control is an often-overlooked yet vital component in the quest of item quality and operational efficiency throughout diverse markets. Personnel training is similarly vital; ensuring that employees are well-informed concerning foam characteristics and control techniques can lead to positive foam monitoring.
While lots of industries face distinct challenges associated to foam control, situation studies expose that tailored methods can dramatically enhance both item quality and operational effectiveness (Foam find more Control). In the pharmaceutical market, for instance, a leading producer implemented a custom-made foam control approach that minimized foam formation during fermentation processes.In final thought, efficient foam control is indispensable to improving product top quality and functional efficiency across various markets